Heat conducting films
(Keratherm®)
The constantly increasing technical demands on electrical and electronic assemblies lead to major challenges in the area of thermal management.
Due to the miniaturization of components and the higher performance of devices, component temperatures would increase significantly without countermeasures, which can lead to the failure of the entire assembly.
In order to increase the longevity of electronic components, heat must therefore be conducted from the heat source (electronics) to the heat sink (e.g. heat sink).
Thermally conductive and electrically insulating intermediate layer materials, so-called Thermal Interface Materials (TIMs), are used for this purpose.
KERAFOL® has developed effective, uncomplicated and cost-effective solutions in this area with the KERATHERM® and KERAMOLD® product ranges.
One of the best-known product groups are the so-called heat conducting films.
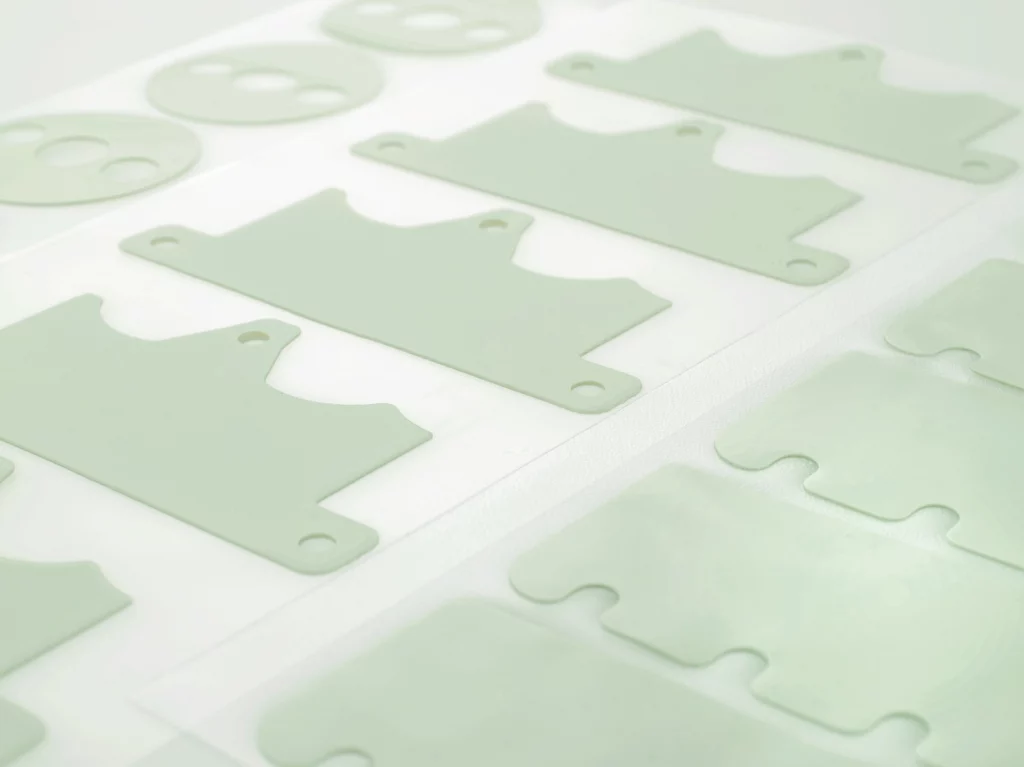
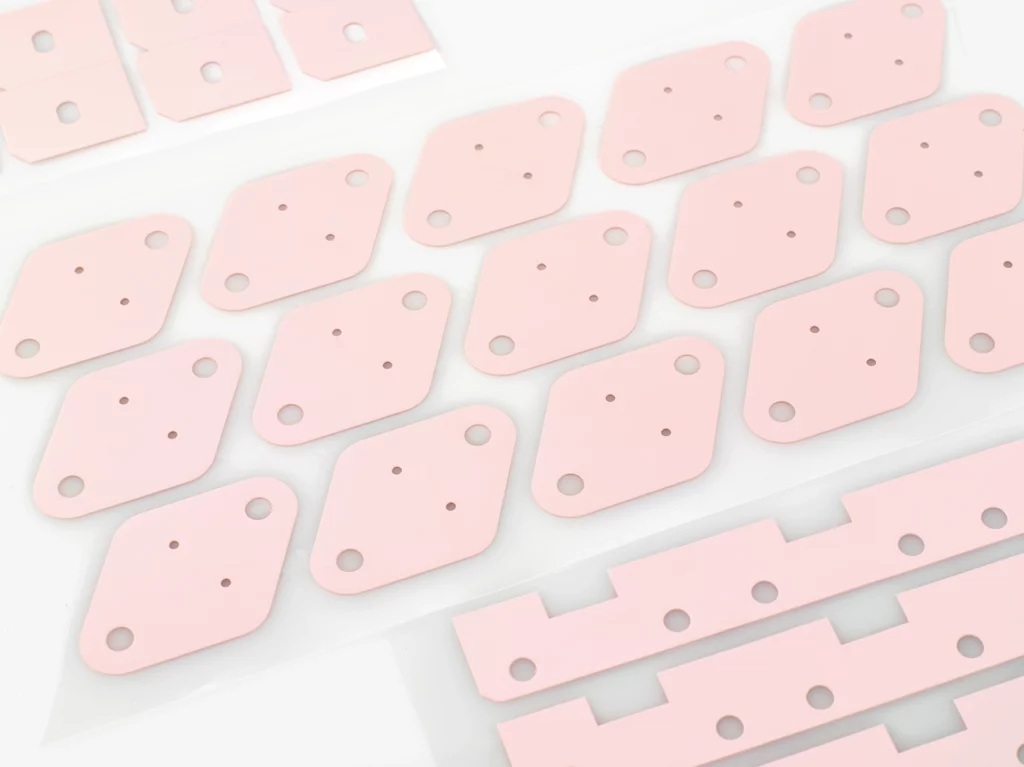
What are heat conducting films?
an explanation
Thermally conductive films (KERATHERM®) are highly thermally conductive and electrically insulating films based on silicone, polyurethane or epoxy.
These materials are particularly suitable for generating an efficient heat transfer from the heat source (e.g. semiconductor) to the heat sink (e.g. heat sink), especially with low component tolerances, due to their low layer thickness of 100 to 500 µm.
The simultaneously very high electrical insulation strength prevents electrical breakdowns and flashovers.
To increase the mechanical stability, certain films can be provided with a glass fiber reinforcement; in addition, a one-sided adhesive coating can be applied as a fixing aid in the application according to customer requirements.
Key Facts
to the thermally conductive films from Kerafol®
- Thermally conductive and electrically insulating at the same time
- Used for small component tolerances and gap dimensions in the range of 0.1 to 0.5 mm
- Various designs possible (with glass fiber reinforcement and/or adhesive coating)
- Available by the meter on rolls and/or specifically cut to size
- Different polymer bases possible, silicone-containing and silicone-free
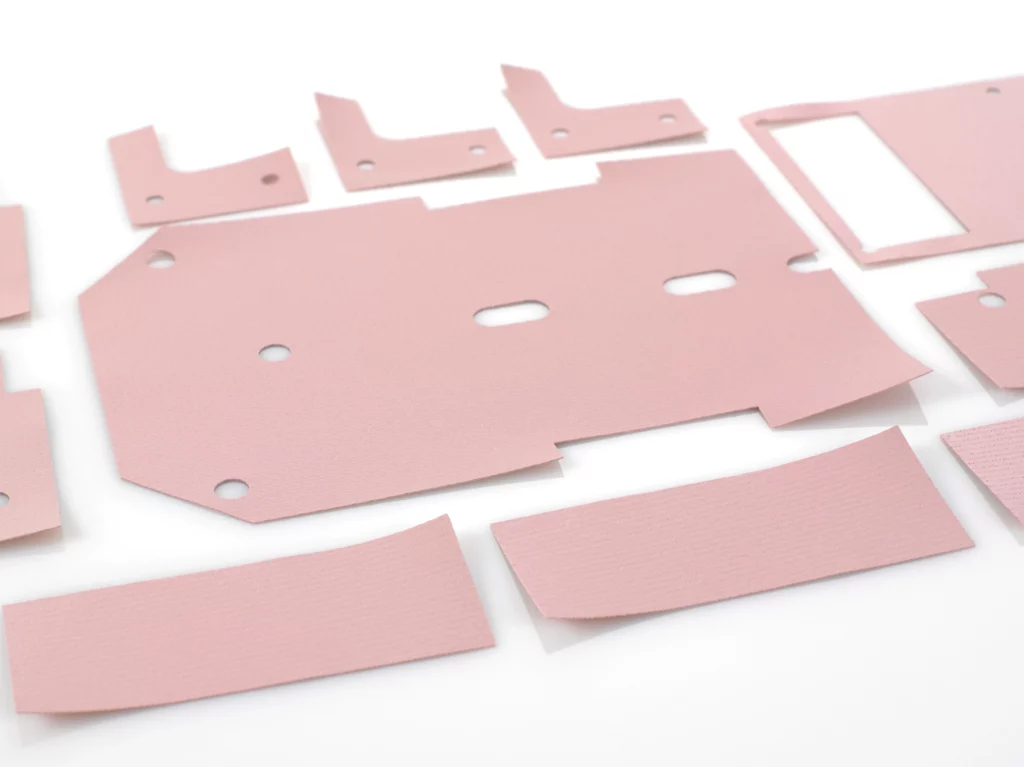
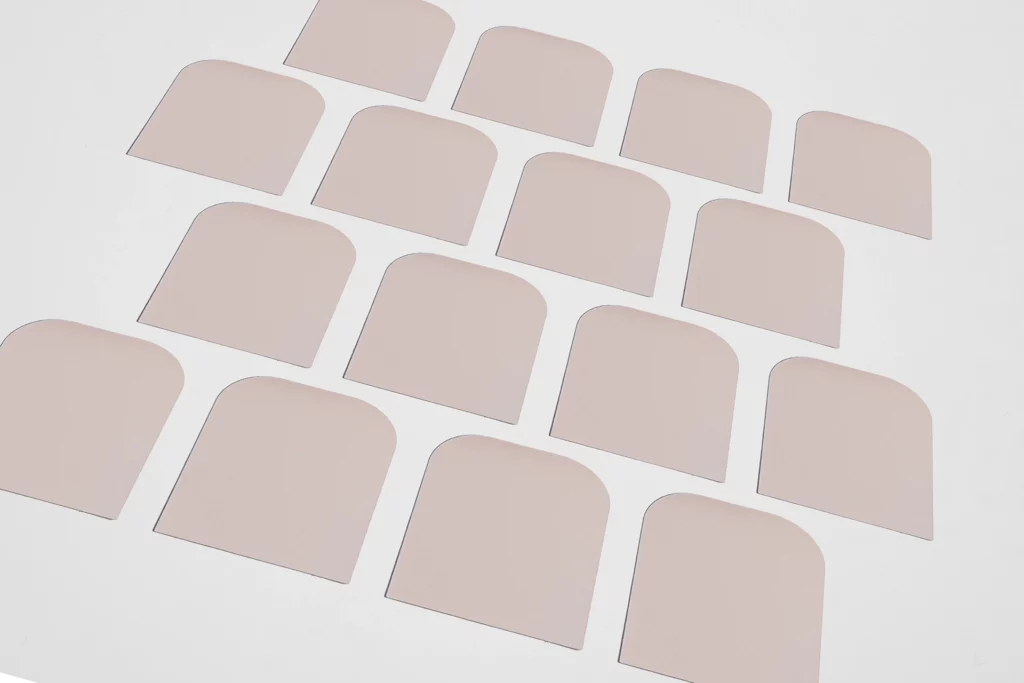
How are heat conducting foils processed?
Application
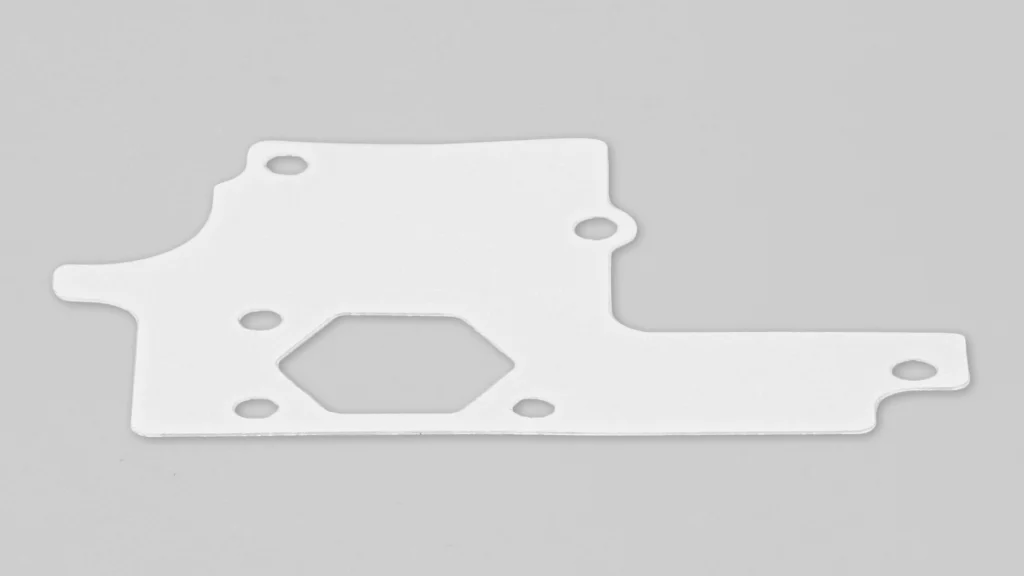
Advantages
of the thermally conductive films from Kerafol®
- Wide range of thermal conductivity (up to 6.5 W/mK) and layer thicknesses (0.1 mm to 0.5 mm) with high electrical insulation at the same time
- Available with glass fiber reinforcement and/or adhesive coating
- Very good thermal properties, even at low contact pressure
- Low Shore hardness (Shore A)
- Good availability
- Available by the meter on rolls and/or specifically cut to size
- Very good long-term and temperature resistance
- Different polymer bases possible, silicone-containing and silicone-free
- 100% Made in Germany
Delimitation
to other products
Compared to gap pads, heat conducting foils are somewhat harder (Shore A instead of Shore 00 range).
Thermal conductive films are a very efficient solution, especially for small gap dimensions and low tolerance chains, due to their low layer thickness and the resulting low thermal resistance.
Heat conducting films have a major advantage over heat conducting pastes, particularly when it comes to handling, as the processing of precisely fitting components is much quicker and easier than is the case with liquid materials.
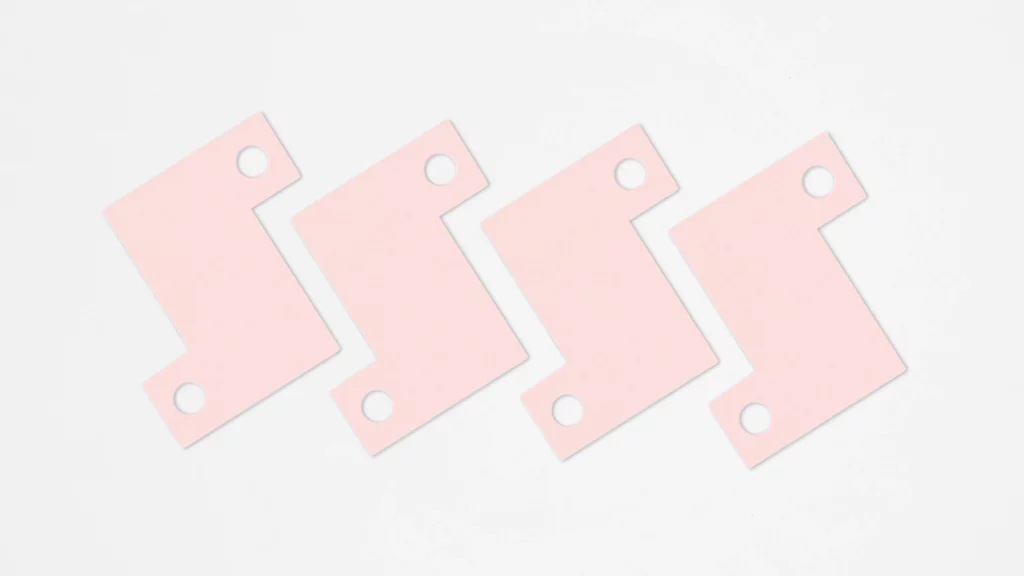
Comparison
Thermally conductive films from Kerafol®
Applications
of heat conducting films
- In many power electronics applications and many other electronic assemblies
- TO housing
- For small component tolerances / gap dimensions