Keralpor 99
Aluminum oxide 99.5 % porous
Keralpor 99 is our standard setter plate, which offers the greatest advantages when used in thermal processes. Due to its low heat capacity, the energy consumption of the kiln is significantly lower when using Keralpor 99 compared to conventional setter plates and kiln furniture. The time and energy required for heating and cooling the kiln is significantly reduced by using KERAFOL® setter plates.
Our customers use these setters for sintering LTCC ceramics, solid oxide fuel cells, SOFC/SOEC components, dental ceramics and for debinding and sintering metal injection molding (MIM) components. The high evenness of Keralpor 99 leads to precise sintering results. Due to the high porosity of 36-38 % of the alumina matrix, gases can freely diffuse through the sintered plate during the debinding and sintering processes. The high purity of the Al2O3 ceramic reduces your post processing effort to a minimum or is not necessary as there are no contact reactions.
Also, no adhesion to the setter occurs during the debinding process. Keralpor 99 can be uses best as a setter plate on your silicon carbide, mullite, corundum and molybdenum kiln furniture.
All sizes up to 310 x 310 mm are available in thicknesses of 1.0 / 1.5 / 2.0 mm.
Please request your customized dimensions and we will produce your Keralpor 99 as quickly as possible.
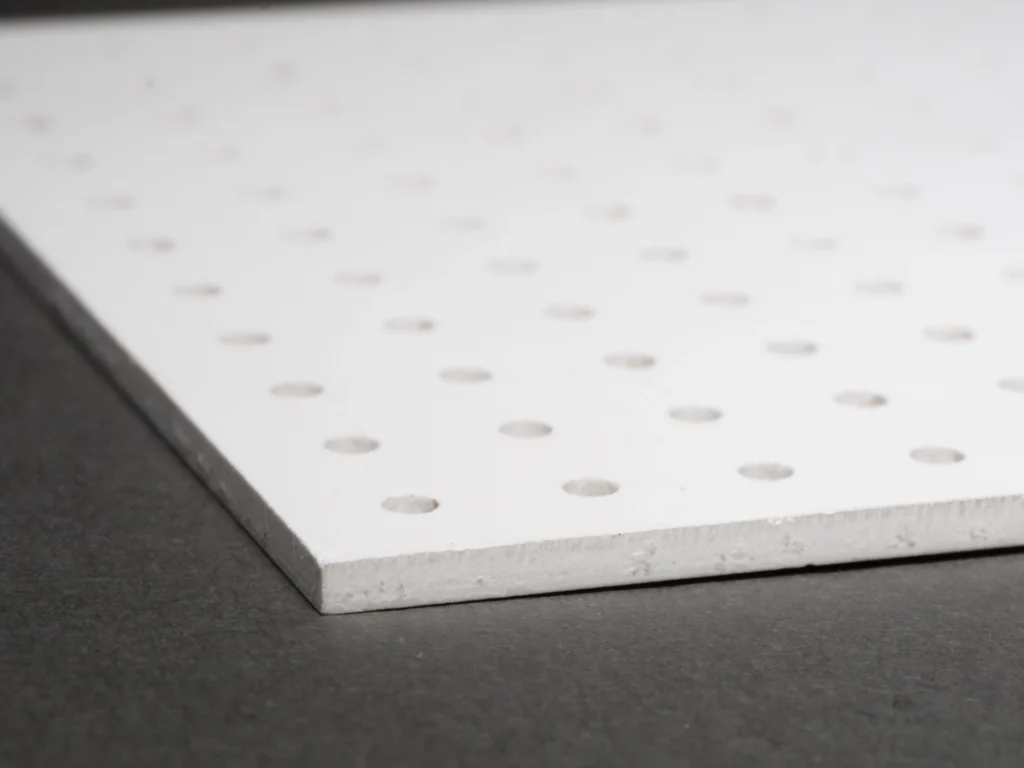
Advantages
from KERALPOR 99
- Dust and particle-free surface
- Homogeneous pore distribution
- Good mechanical strength compared to the high porosity
- Material can be cut by laser or waterjet
- Very good planarity and surface quality
- Large customized dimensions of the setter possible
- Gases and liquids can freely diffuse through the sintered substrates
Applications
Keralpor 99
- Setter plates for metal injection molding (MIM)
- Setter plates for ceramic or dental ceramic production
- Gas-permeable membranes for sensors